This takes film to the next level:
Super special, for maximum productivity.
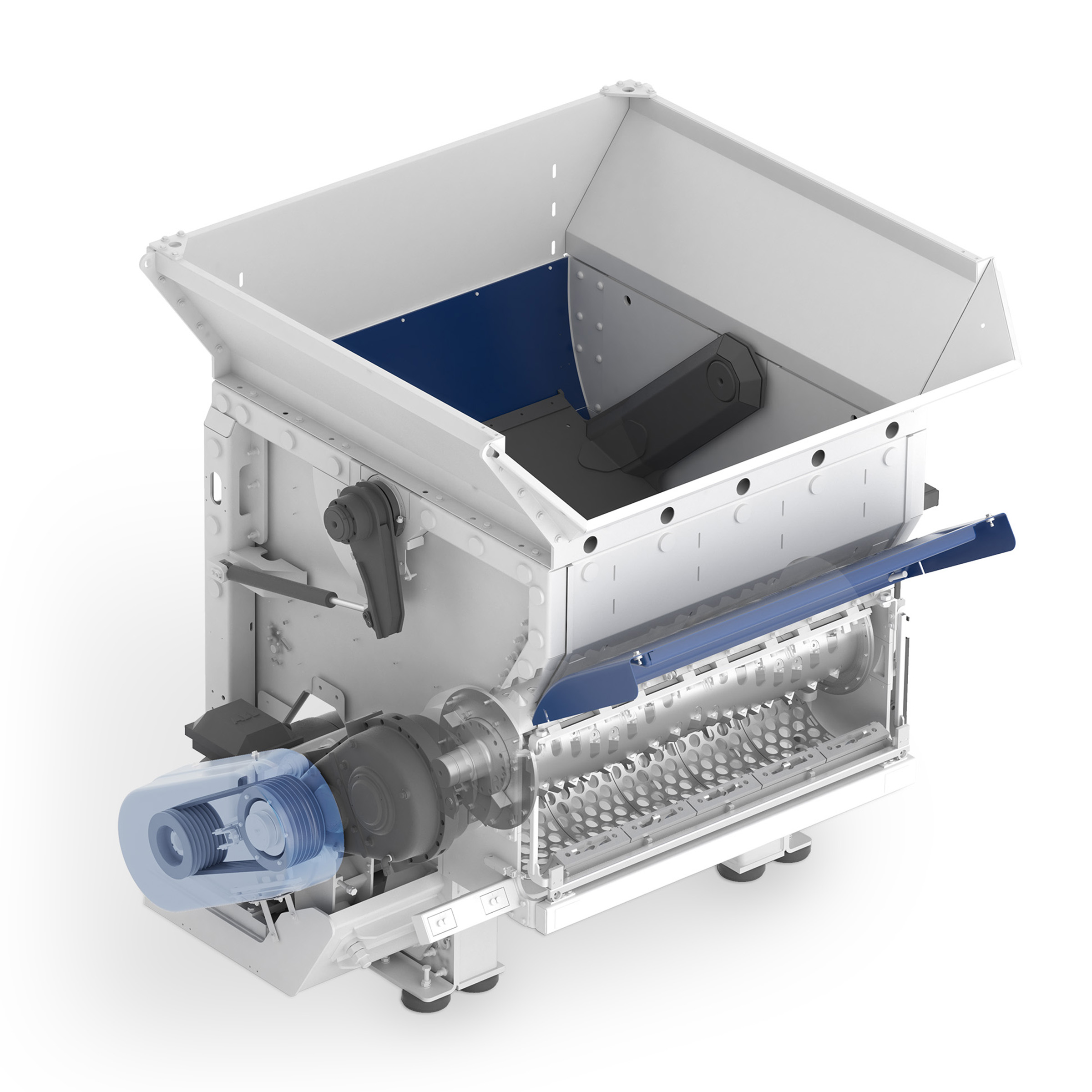
1 | Powerful gear drive
POWERFUL GEAR DRIVE
- ROBUST, HIGH-TORQUE GEAR DRIVE the effective shredding of e.g. rigid plastics, fibres, nets and big bags
- POWERFUL SHREDDING due to high-torque, high-performance motors
- OPTIMUM MACHINE PROTECTION thanks to the safety clutch and the drive unit’s instant mechanical disengagement in the event of incidents
- GLOBAL AVAILABILITY of all easy-change standard part
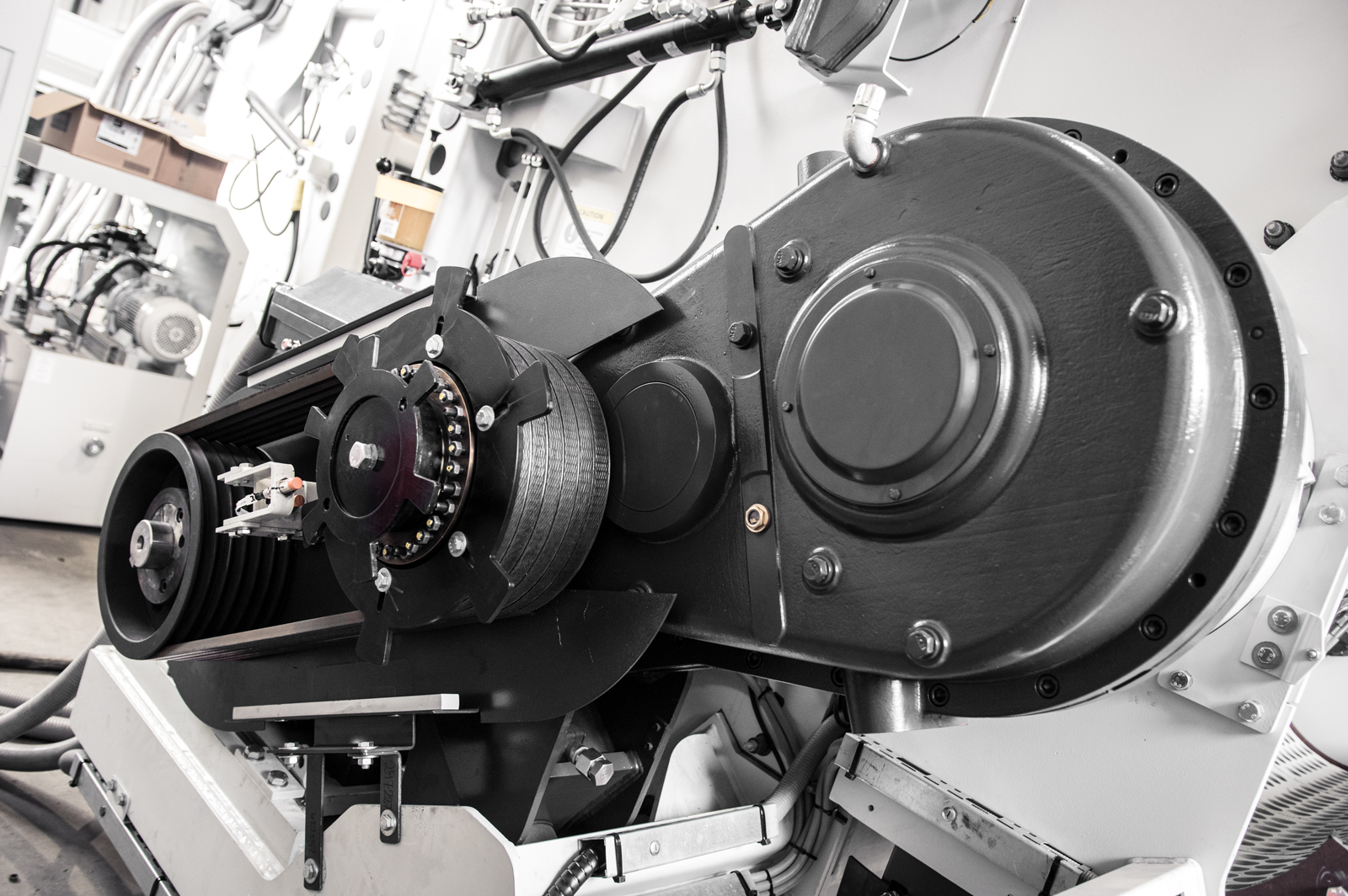
2 | Maintenance door
The hydraulically operated, inward-opening maintenance door allows you to quickly and safely access the cutting system for maintenance work or swiftly remove foreign objects with minimum material leaks.
- FAST CLEANING AND READINESS FOR DIFFERENT INPUT MATERIALS thanks to easy access to cutting unit and pusher
- ENJOY CONVENIENT ACCESS to the rotor and counter knives for a fast knife exchange with the maintenance door at position 3
- QUICK AND CLEAN REMOVAL OF NON-SHREDDABLES with the maintenance door at position 2
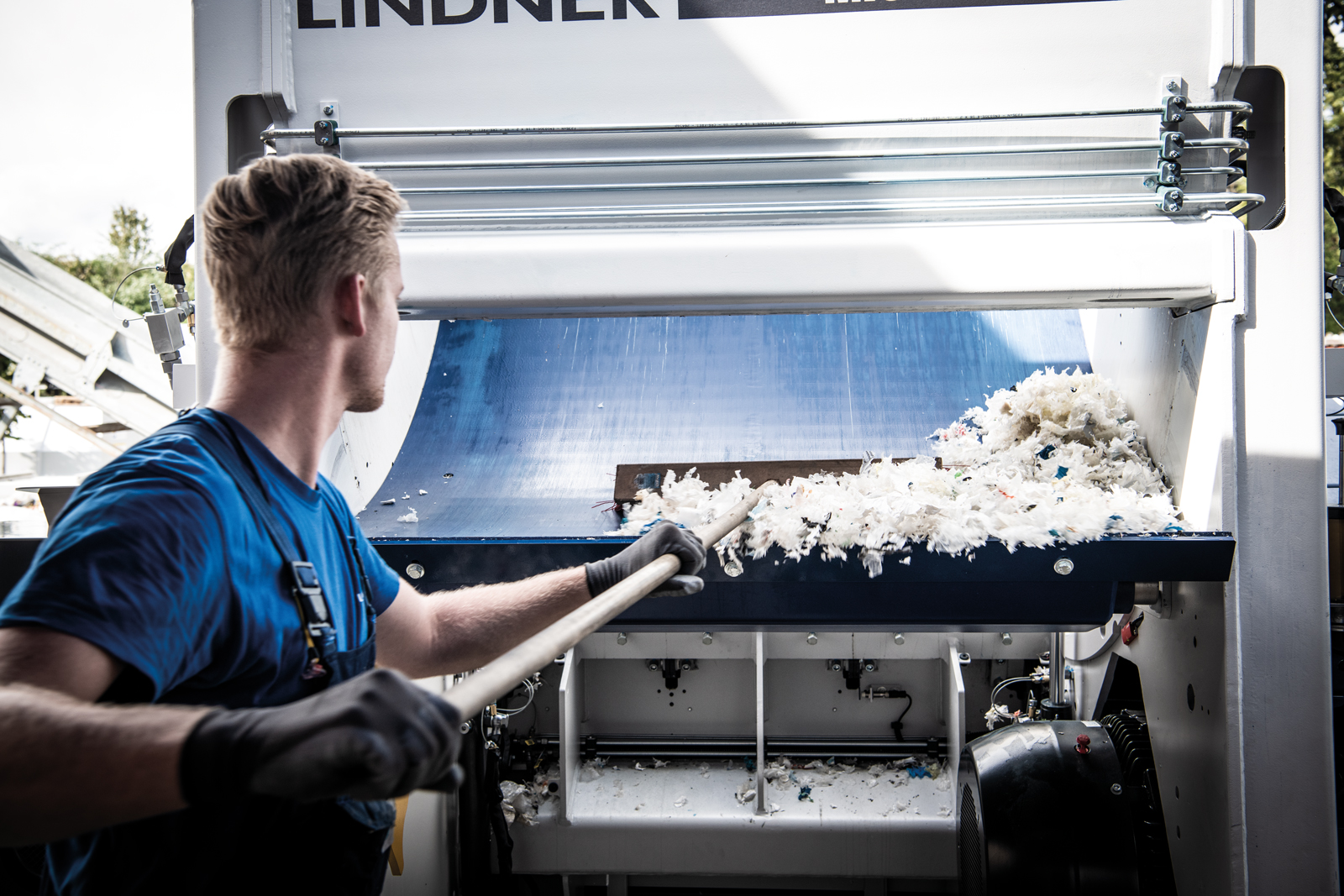
3 | Cutting unit
MONO FIX TECHNOLOGY
The Mono Fix system allows knives and knife holders to be changed with just one screw. A combination of different pointed and flat knives, as well as blind plates and special counter knives, can also be attached to the rotor. The result:
- MAXIMUM FLEXIBILITY of the cutting unit
- MAXIMUM ADAPTION to input and particle size
Also, the knives 65P (second image) can be changed easily thanks to the screw fitting. They are exceptionally robust, offering exceptionally accurate cutting.

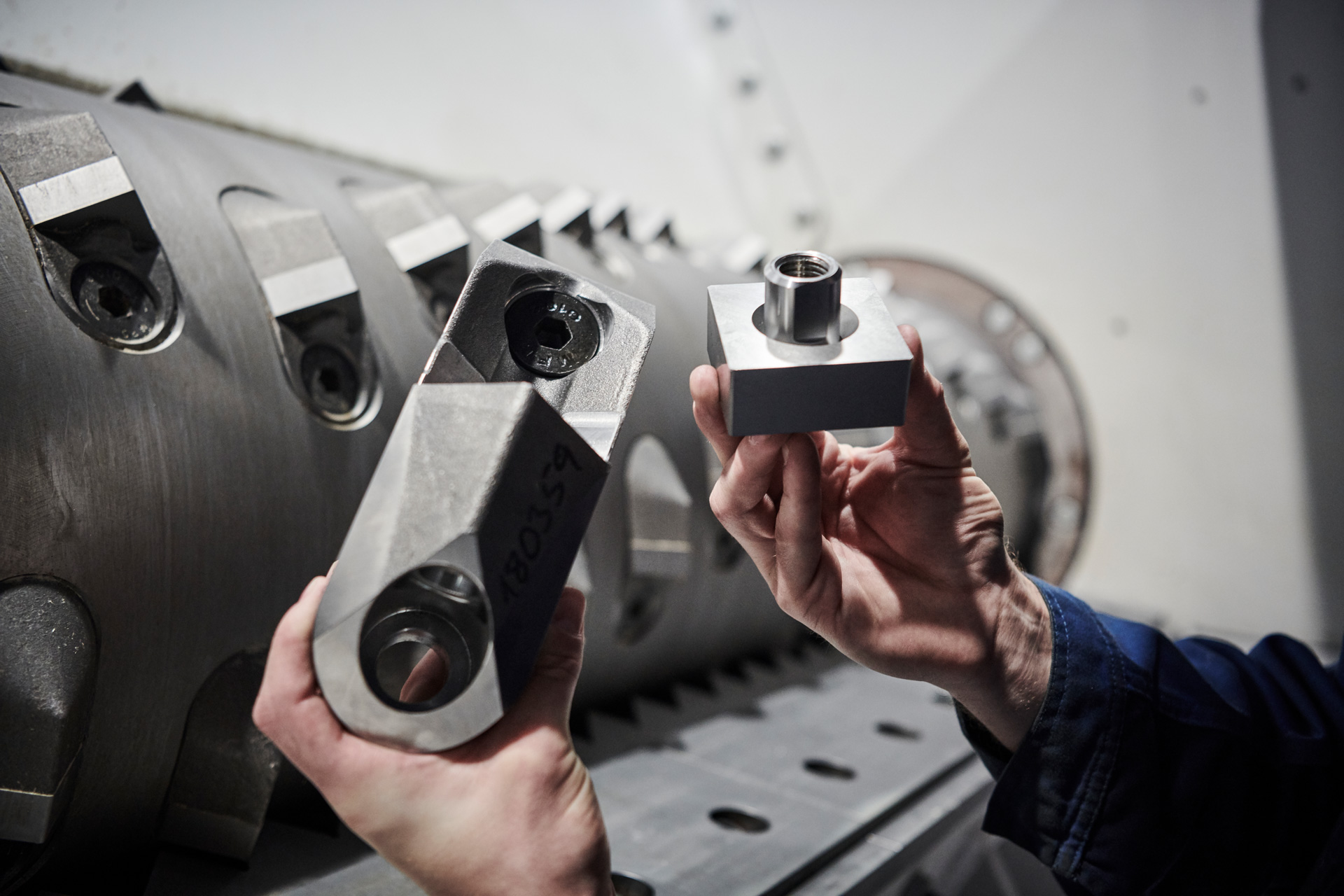
4 | Internal pusher
Lindner's original: tried and tested a thousand times over, our internal pusher allows for easy and secure machine feeding. Our years of experience and continuous development have left their mark on its distinctive design.
- CONSTANT SHREDDING due to uniform material feeding
- MAINTENANCE-FREE thanks to the absence of guide elements
- EASY FEEDING with a completely internal construction
- NO JAMMING as a result of additional comb and sealing bars
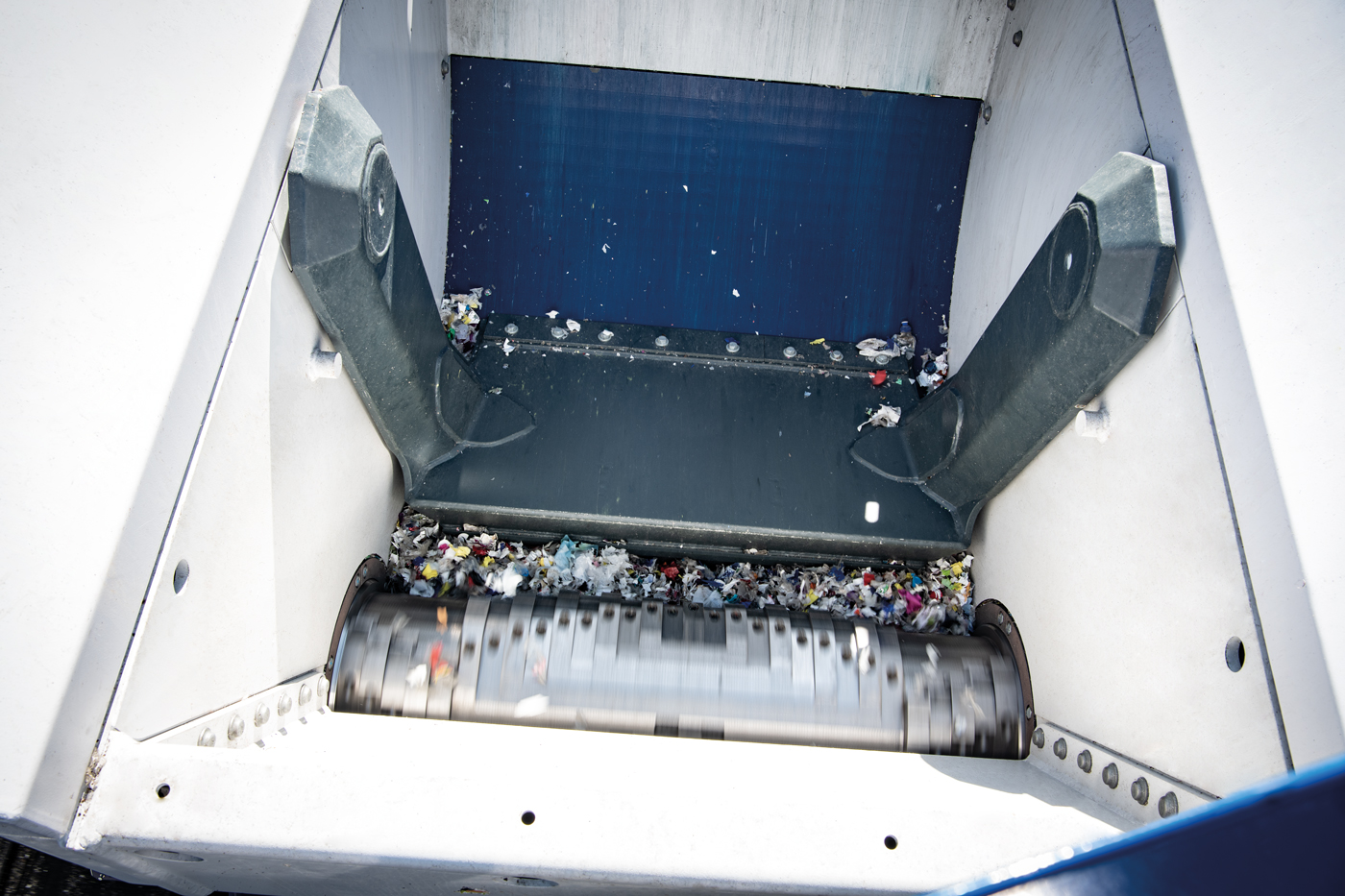
5 | Plug & go screen unit
The swivel-mounted, hydraulically operated screen unit allows for easy and comfortable access for maintenance and refitting. The screens are available with various mesh widths and can easily be changed by hand by just one person – so you can quickly customise the shredder to the particle size you need.
- FLEXIBLE OUTPUT SIZES possible with our quick-change screen units in various hole sizes
- EASY SCREEN CHANGE thanks to their swivel-mounted, hydraulically operated, modular design
- EXTREMELY SAFE OPERATION with the electromagnetically locked screen access point
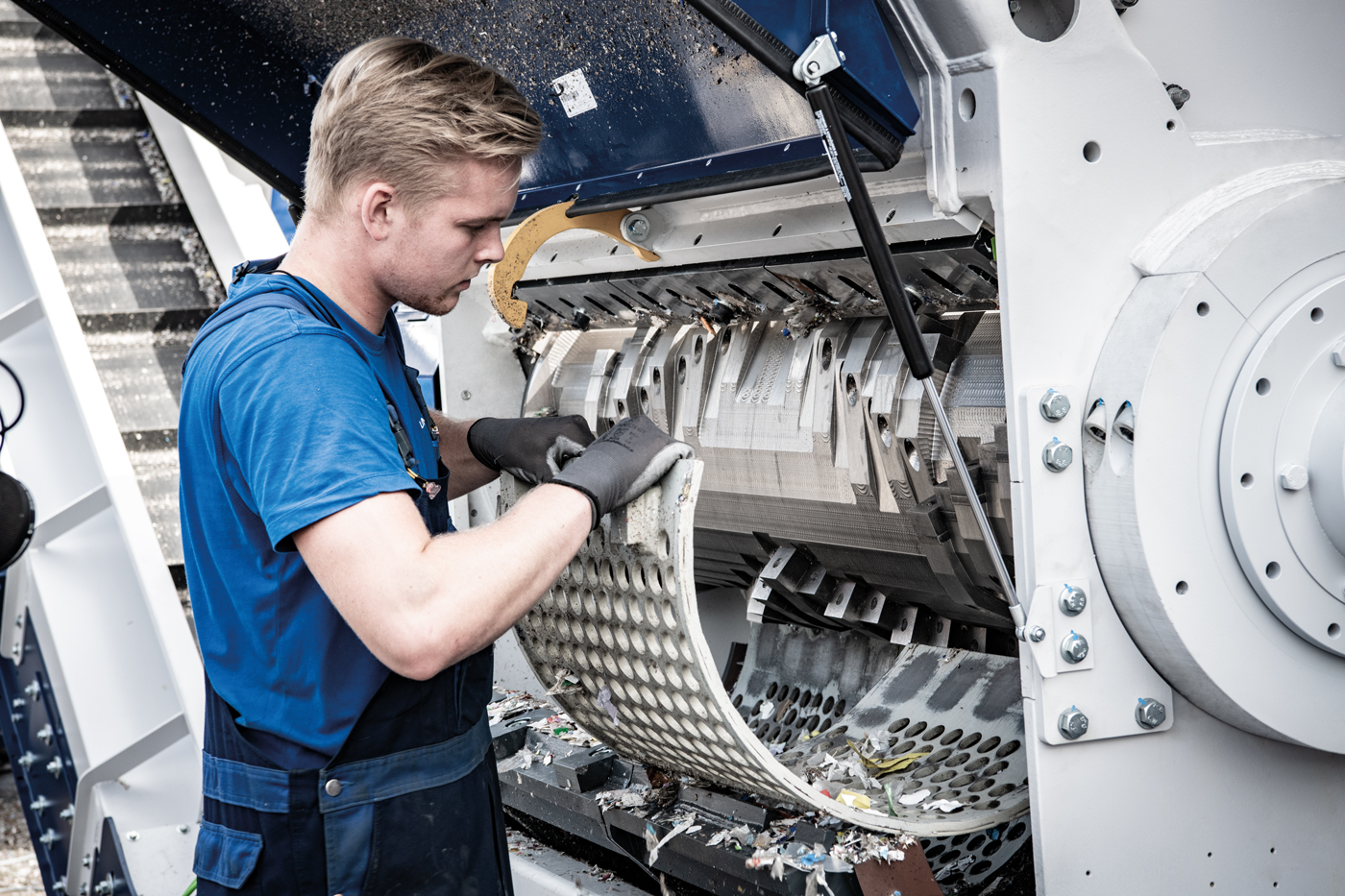
Fire prevention
THAT’S HOW TO PLAY IT SAFE
Lindner’s modern out-of-the-box FPS solution automatically detects and cools over heated particles in the material stream directly on the discharge conveyor, effectively preventing possible sources of fire. The system adapts the cooling process to the hazardous situation to ensure the facility operates optimally at all times.
- Precise detection of overheated materials
- Comprehensive monitoring of the entire cooling section
- Cooling process adapted to the hazardous situation
- Independent cleaning of the infrared sensors
- Temperature resistant and robust thanks to a special insulation system
- Highly flexible modular design
Watch video here!
Water sprinkling system
- To remove dust from the filling area
- 4 spray nozzles positioned in the enclosed hopper
- Switch it ON/OFF using the control panel
- Machine piping incl. central water supply
- Incl. heating system & piping insulation
Rotor cooling
Complete rotor cooling system
- Ideal for shredding temperature-sensitive materials
- Prevents clumping and melting of the final product
- Incl. cooling aggregate
- Water connection pipe: 1"
Find your ideal solution and
Connect with us
INPUT & OUTPUT MATERIALS
FILM
HDPE Plastics
PAPER
CONFIDENTIAL DATA
KEY FEATURES
LINDNER ADVANTAGES
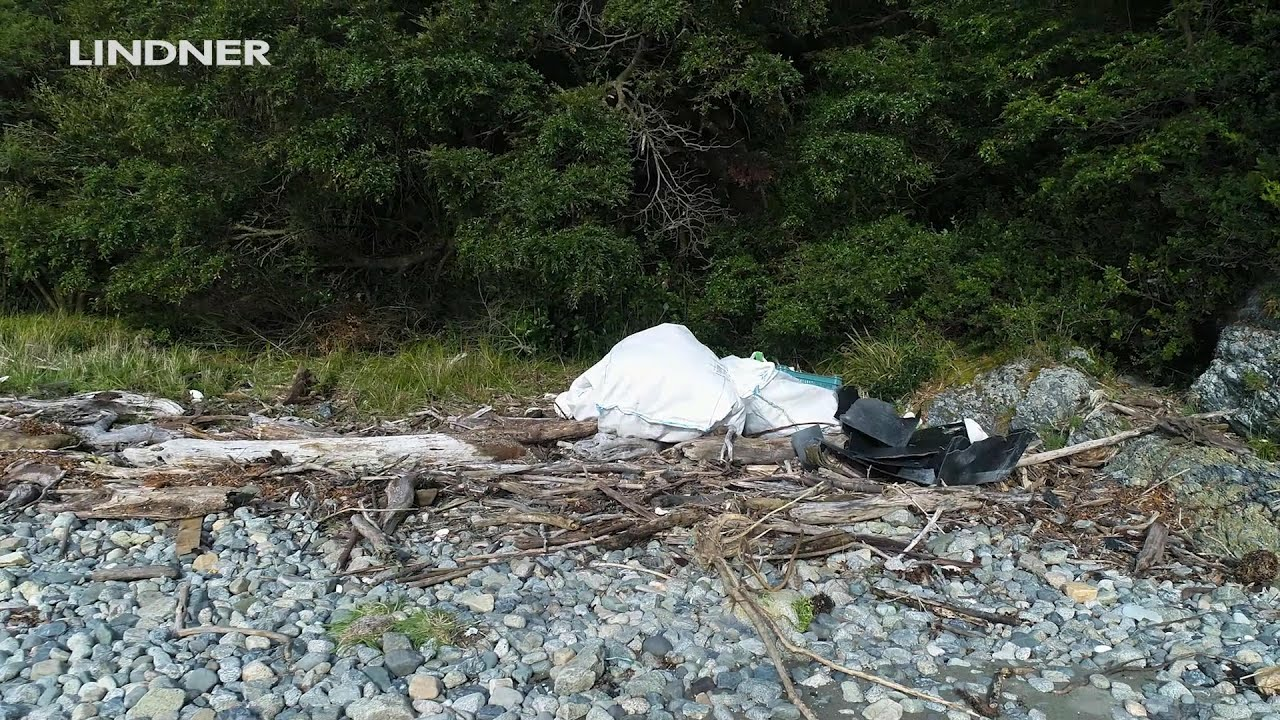
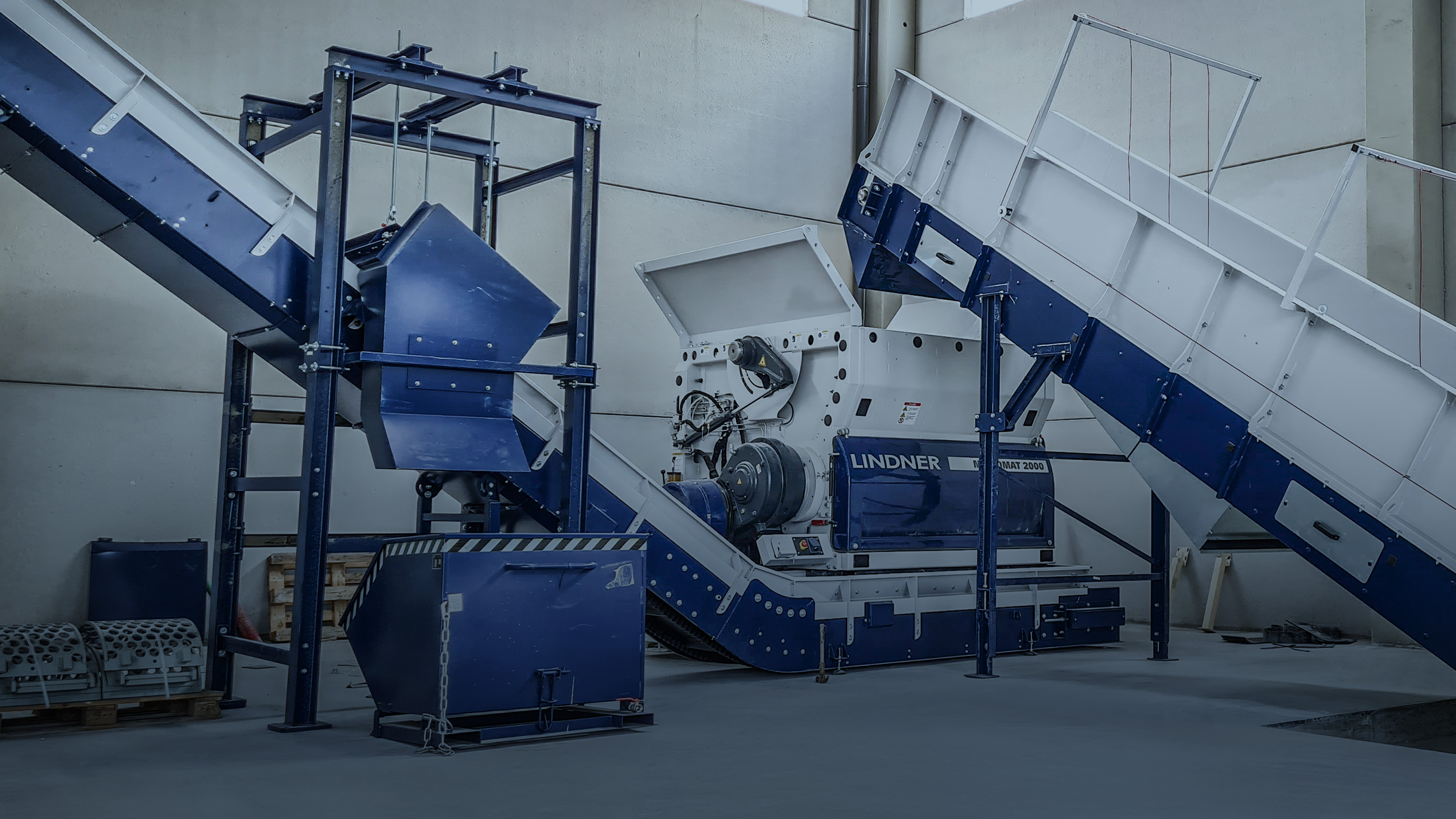
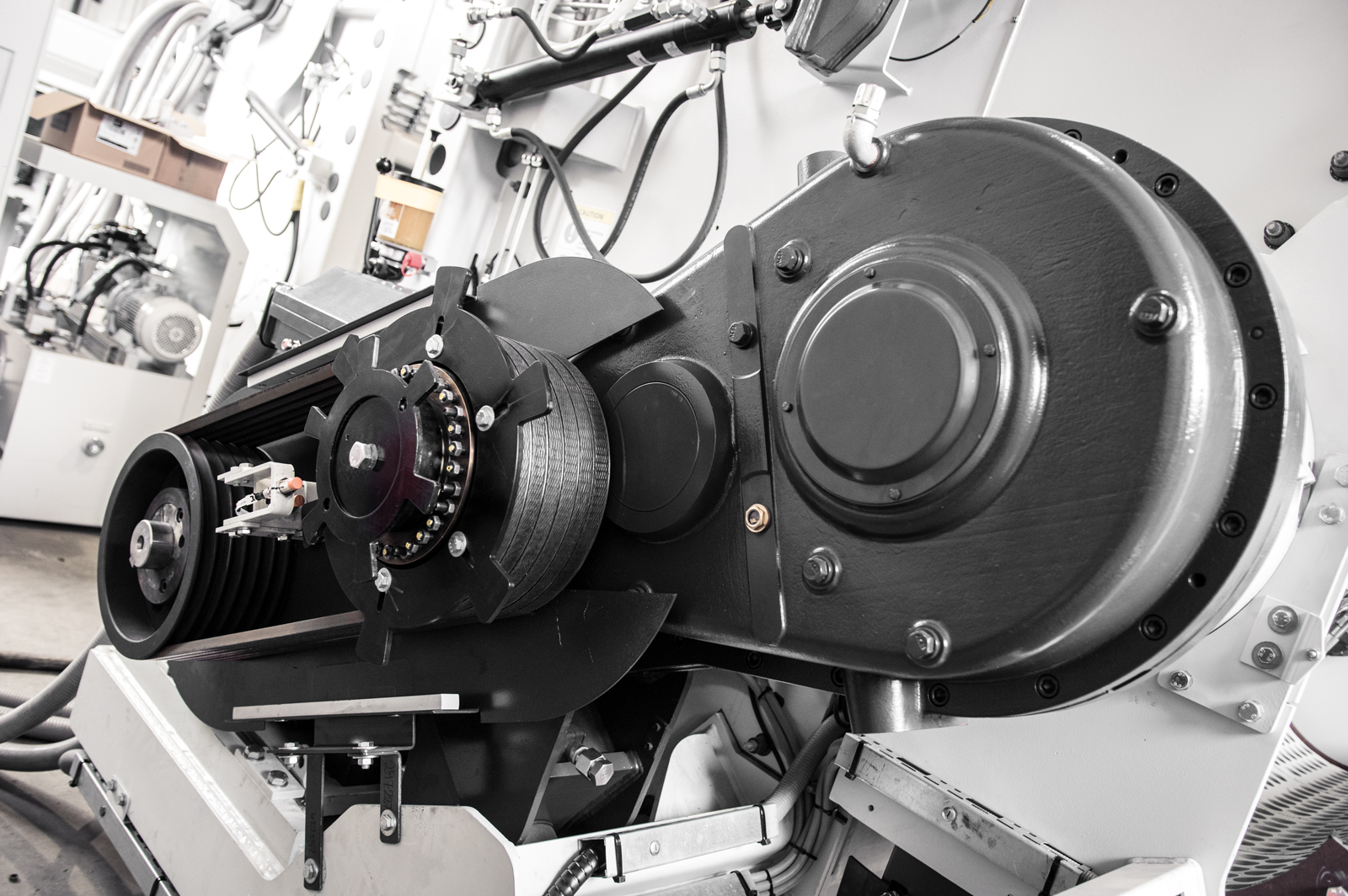

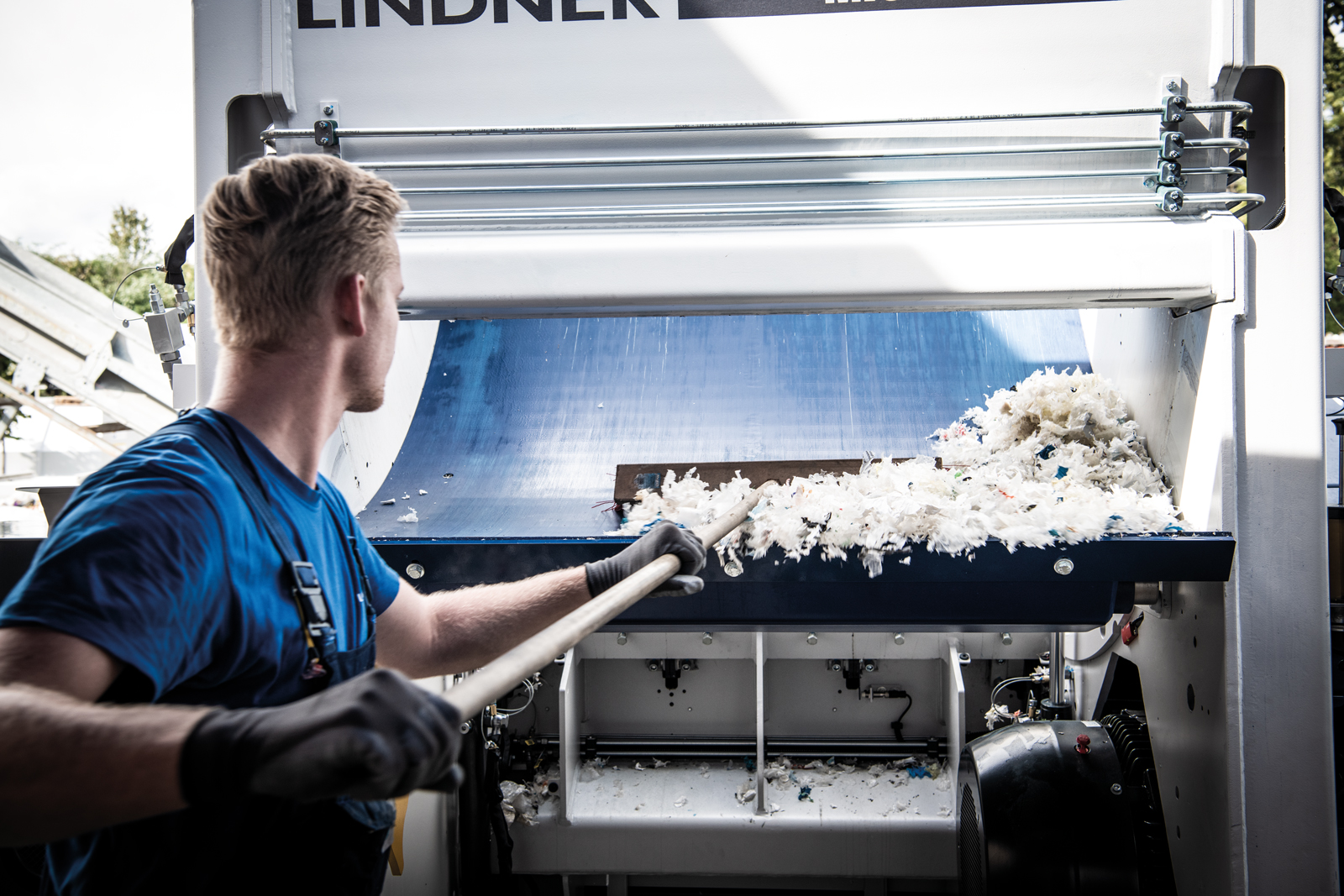
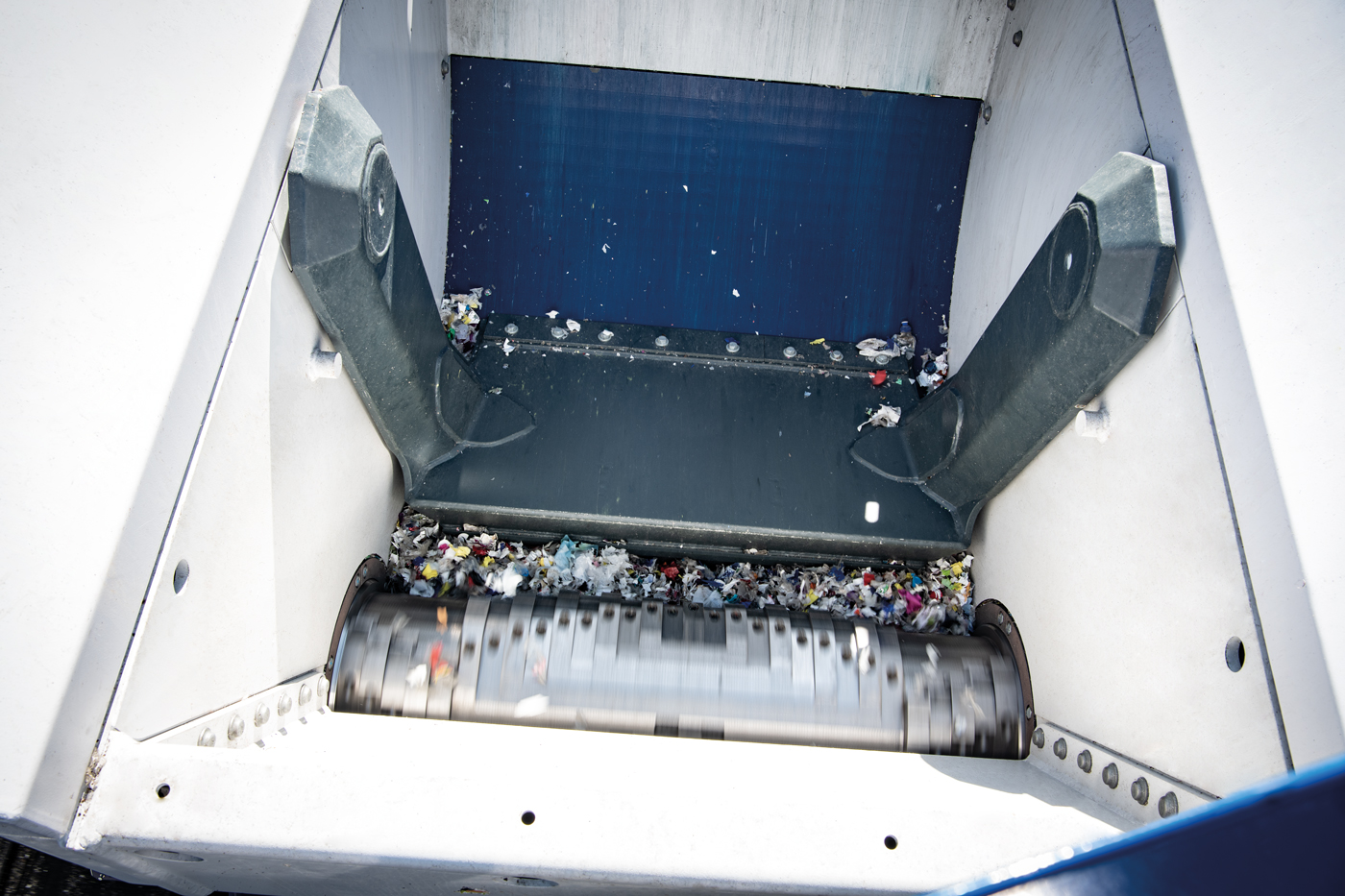
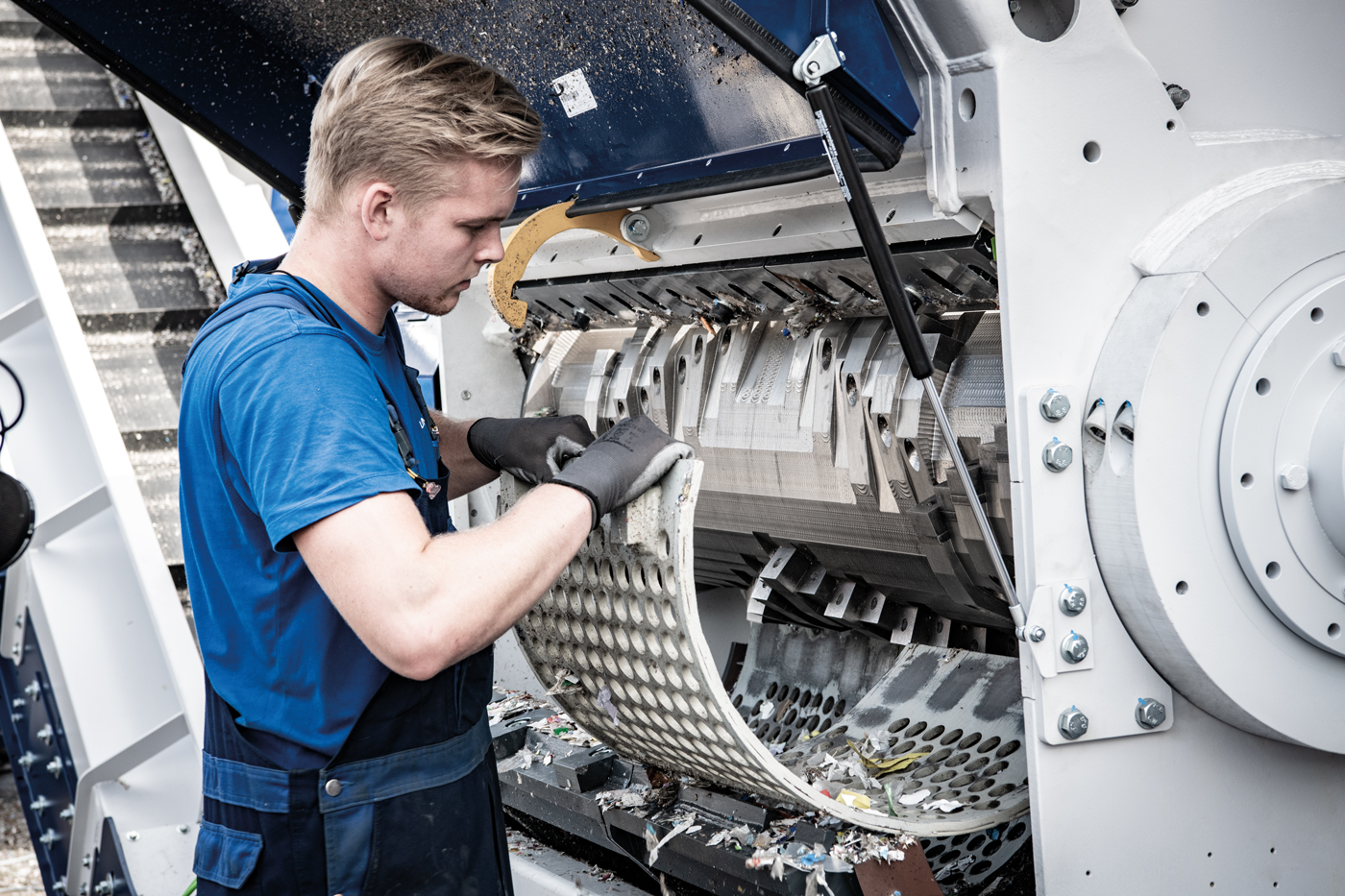