MERAK: SHREDDING AT ITS BEST
UNIVERSAL GENIUS MEETS EFFICIENCY.
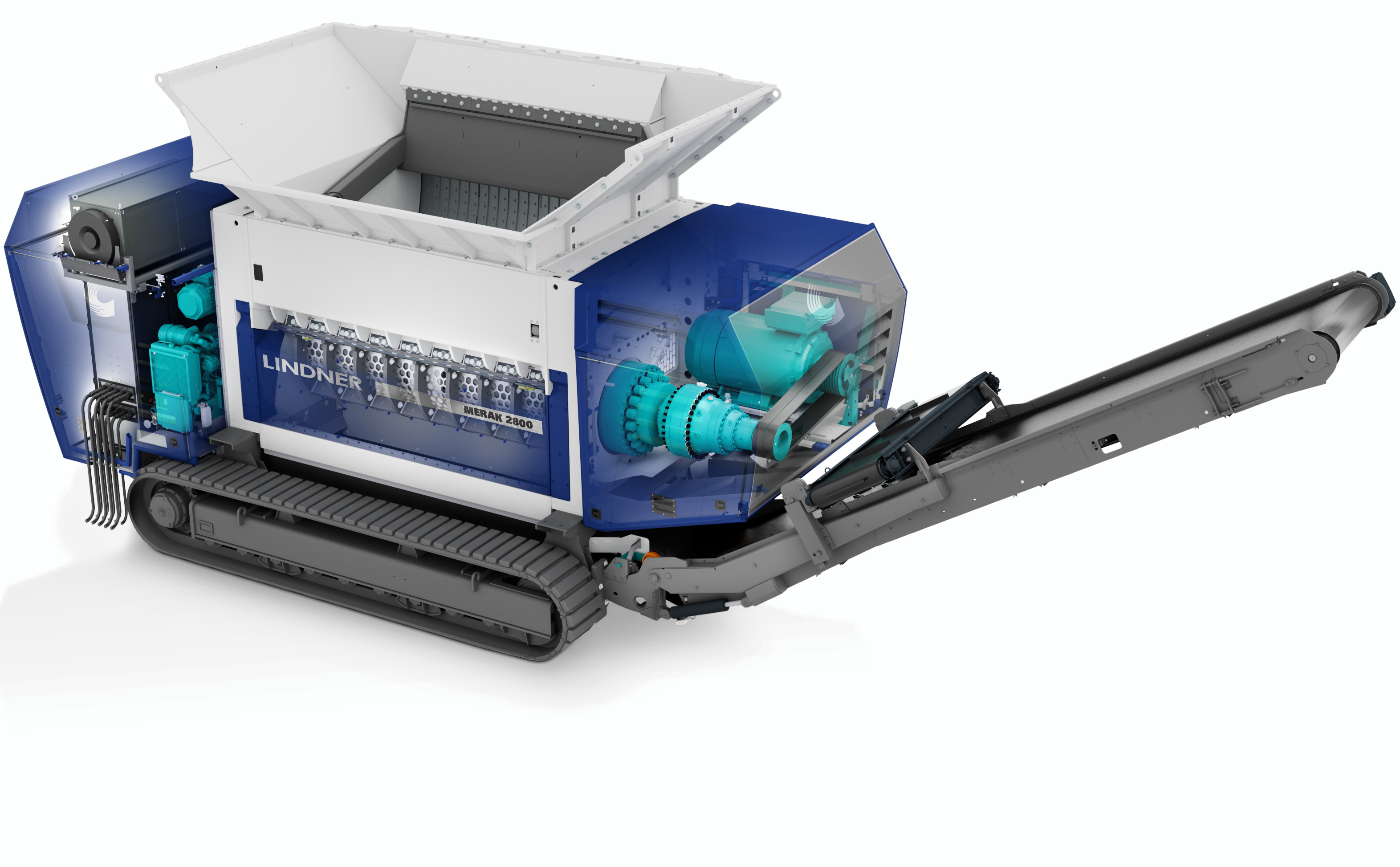
1 | Internal pusher
Lindner's original: tried and tested a thousand times over, our internal pusher allows for easy and secure machine feeding. Our years of experience and continuous development have left their mark on its distinctive design.
- CONTINUOUS SHREDDING due to smooth feeding
- DELIGHTFULLY MAINTENANCE-FREE thanks to the absence of guide elements
- EASY FEEDING with a completely internal construction
- NO JAMMING as a result of additional comb and sealing bars
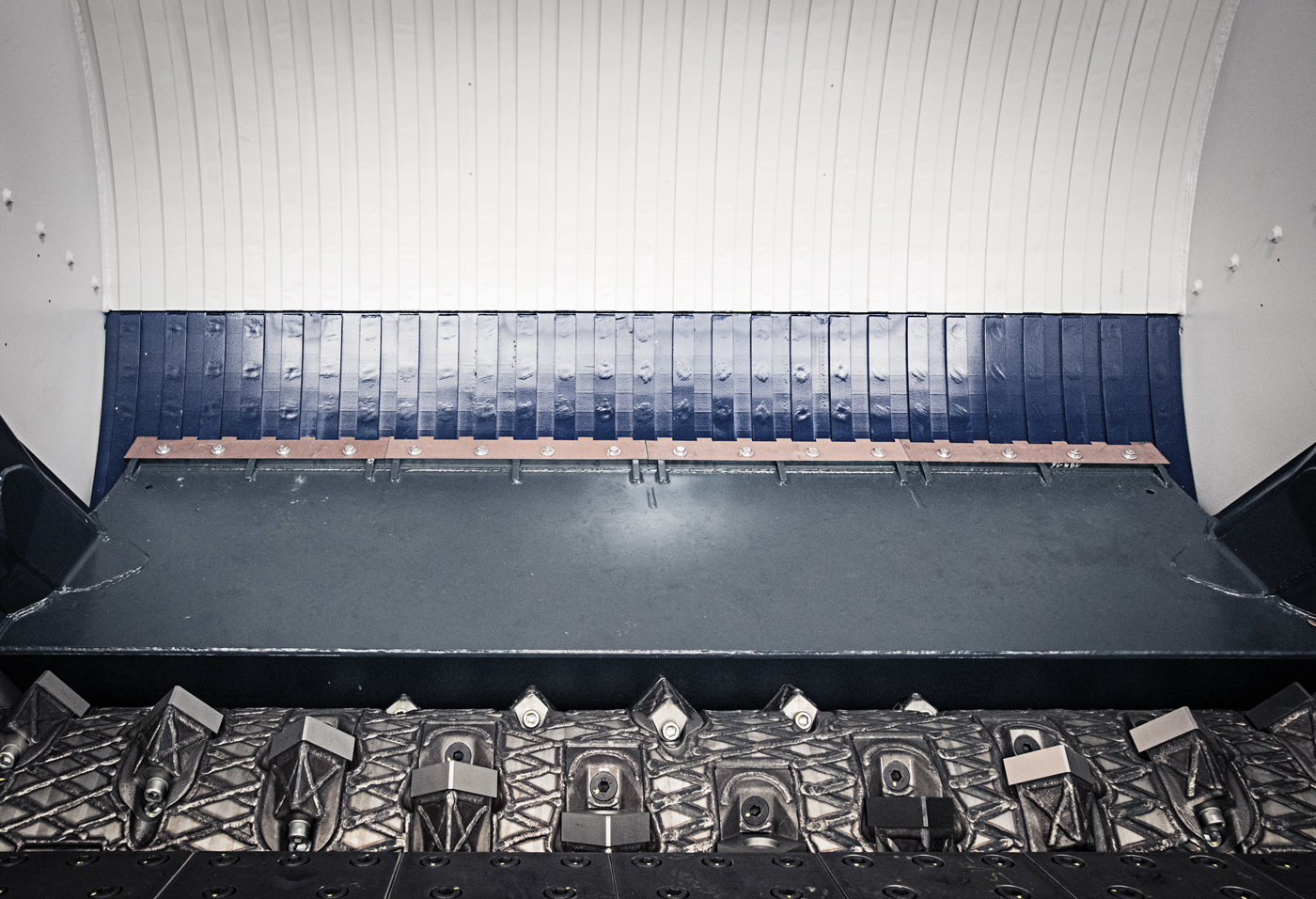
3 | Plug & go screen unit
The swivel-mounted, hydraulically operated screen unit allows for easy and comfortable access for maintenance and refitting. The screens are available with various mesh widths and can easily be changed by hand by just one person – so you can quickly customise the shredder to the particle size you need.
- FLEXIBLE OUTPUT SIZES made possible with screen units in various hole sizes
- EASY ACCESS FOR MAINTENANCE AND FITTING due to the swivel-mounted, hydraulically operated design
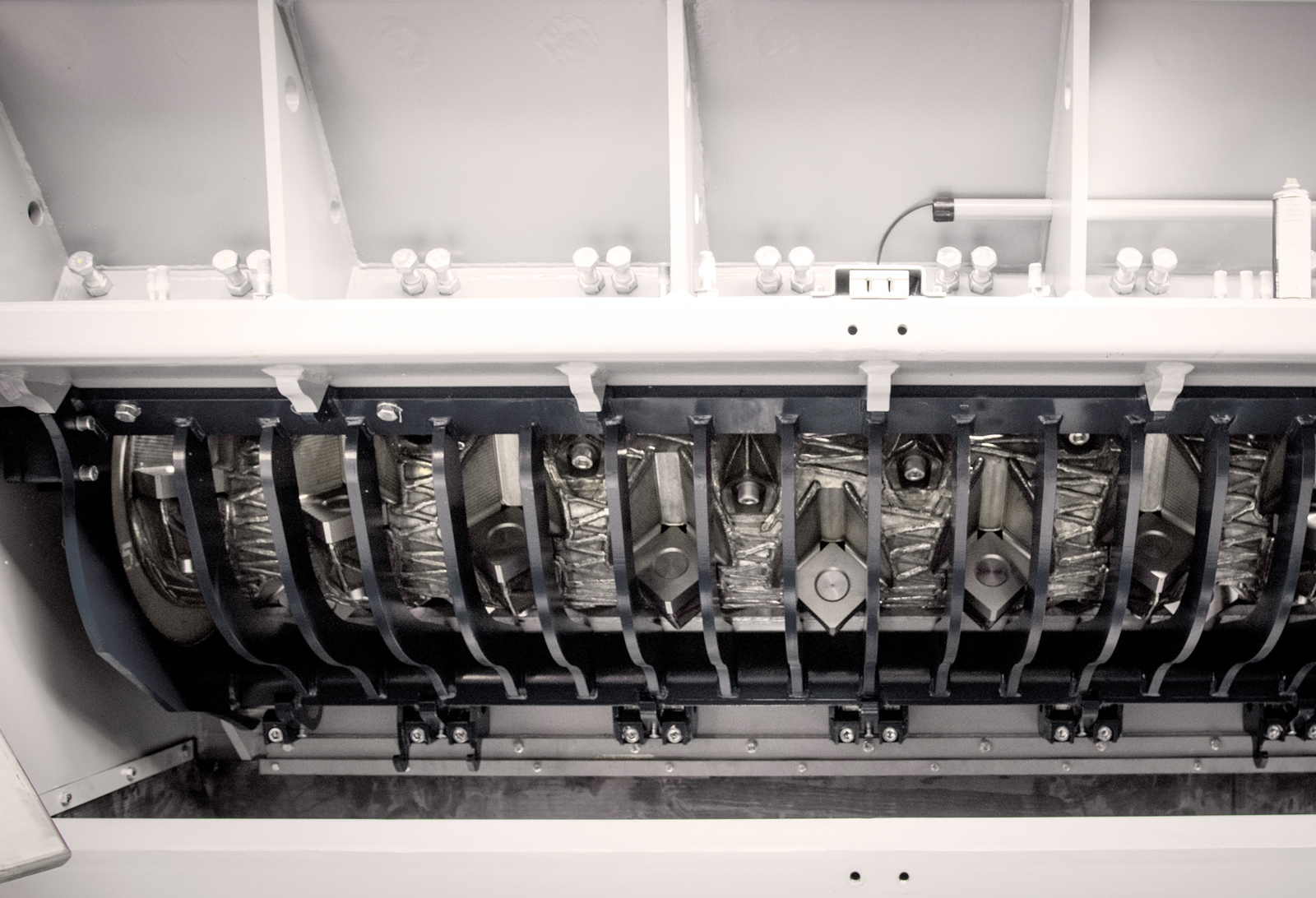
7 | Material Output & FE Metal Separator
The integrated single-belt discharge conveyor is powered hydraulically and might be completely folded away. The height of the conveyor belt can be easily adjusted during operation by simply lifting the belt from the wheel loader during shredding. For particularly heavy materials such as light scrap and tough commercial waste, the conveyor belt can be reinforced with steel.
- FERROUS METAL SEPARATION with an optional integrated over-belt magnet
- CONSISTENT OUTPUT with our smart double tilting hopper system
- LOW DUST EMISSIONS due to the hydraulic height-adjustable conveyor belt, which can even be adjusted during operation
Autom. belt tensioning
Lindner ATB – automatic belt tensioning system
- Ensures optimum power transmission at all times
- Belt exchange using a hydraulic tensioning device
- Self and preventive monitoring
Water sprinkling system
- To remove dust from the filling area
- 4 spray nozzles positioned in the enclosed hopper
- Switch it ON/OFF using the control panel
- Machine piping incl. central water supply
- Incl. heating system & piping insulation
ADDITIONAL WEAR PROTECTION PACKAGE CUTTING SYSTEM
- Ideal for shredding particularly abrasive material
- Rotor hardfacing
- Knifeholder hardfacing
FE metal separator
- Permanent over-belt magnet for ferrous metal separation
- Fitted above the conveyor belt
- Hydraulically height-adjustable
- Incl. discharge chute
Find your ideal solution and
Connect with us
INPUT MATERIALS
C&I WASTE
WASTE WOOD
Railroad Ties
Plastic Container
Plastic Pipes
Plastic Rolls
Mattresses
Carpets
Window Frames
Car Tires
LINDNER ADVANTAGES
CUTTING SYSTEMS