The Urraco 5000EK shredder:
Unleashing Uncompromised Electric Precision.
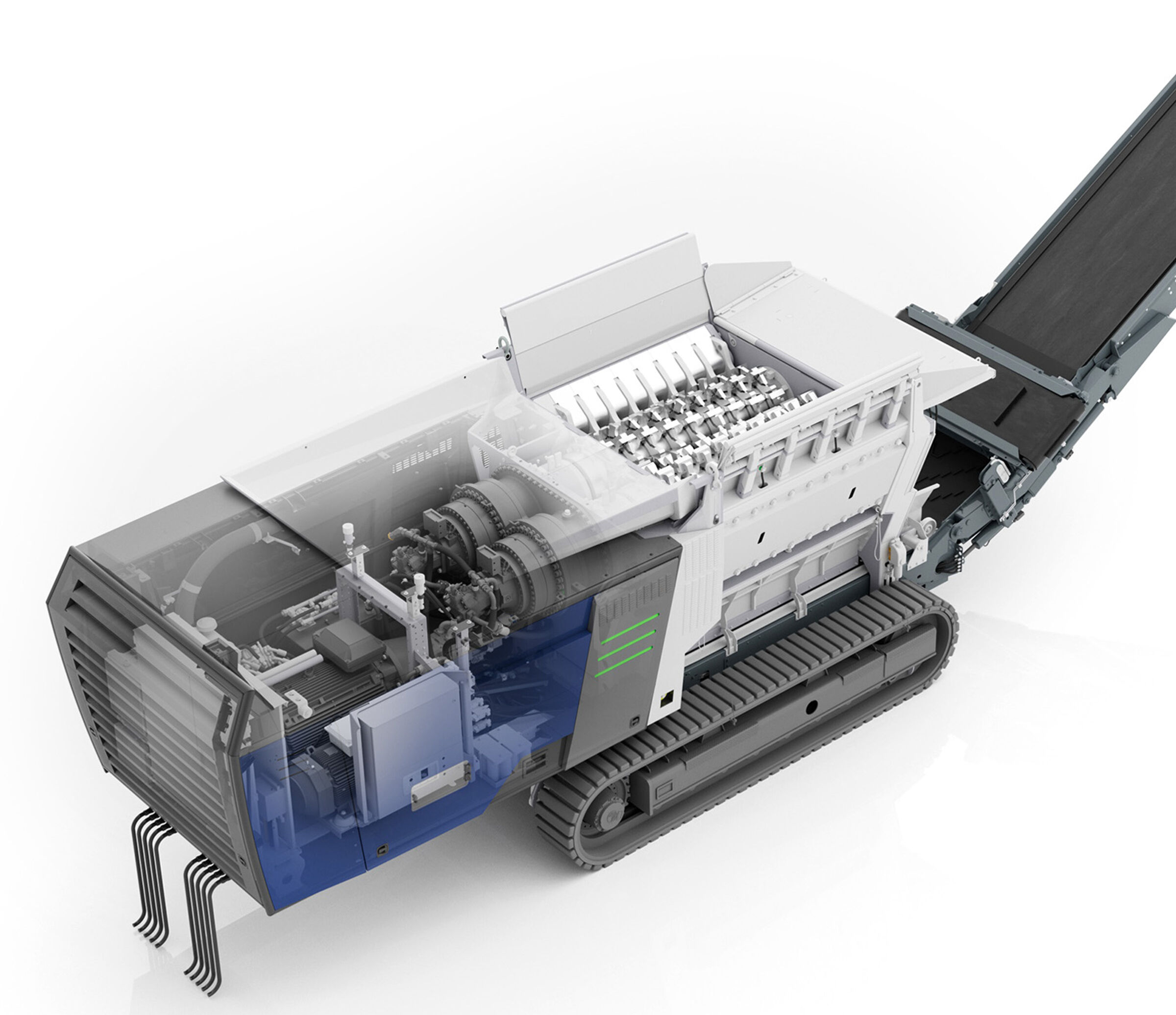
1 | Twin-shaft cutting system
Our Urraco 5000’s slow-speed twin-shaft cutting system ensures aggressive intake and guarantees highly efficient shredding. Depending on the shaft selected, even the toughest materials such as railway sleepers and light scrap metal can be processed safely and effectively.
- INCREDIBLY PRODUCTIVE thanks to aggressive intake and synchronously running shafts
- ADAPTS PERFECTLY TO THE MATERIAL thanks to shaft pairs available in different designs
- MAXIMUM RESISTANCE with our fully welded cutters, rippers, scrapers and breaker bar
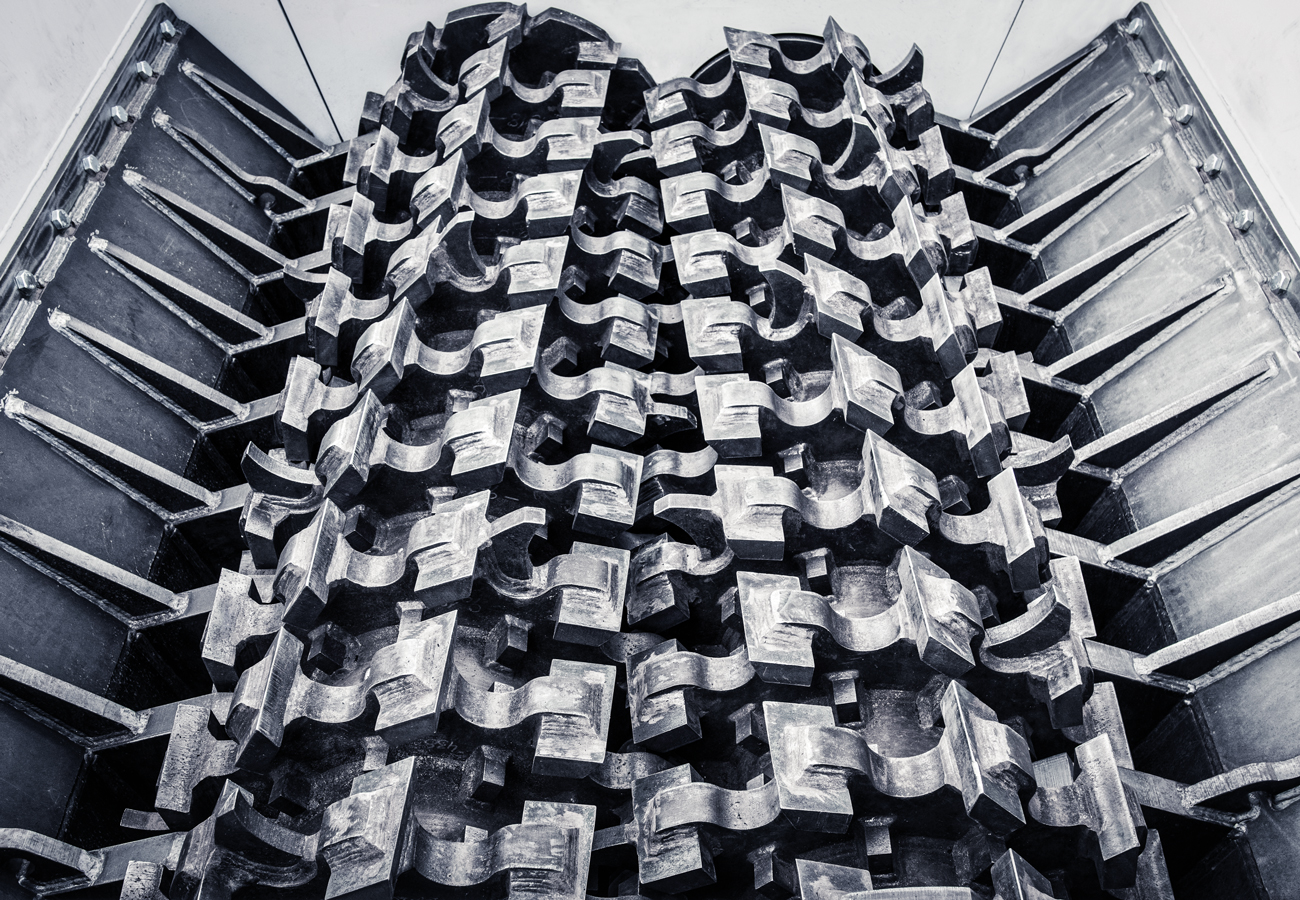
2 | Powerful electric engine
Electro-hydrostatic drive 355kW (+45kW auxiliary functions) with self-regulating hydraulic circuit and electronic mobile controller and independent track drive with Diesel aggregate 37kW.
- INTEGRATED CONTROL CABINET and plug & play electric connections
- COOLING SYSTEM incl. reversible fan for automatic cooler cleaning
- ROBUST HOUSING COATED in line with corrosion class C2-M
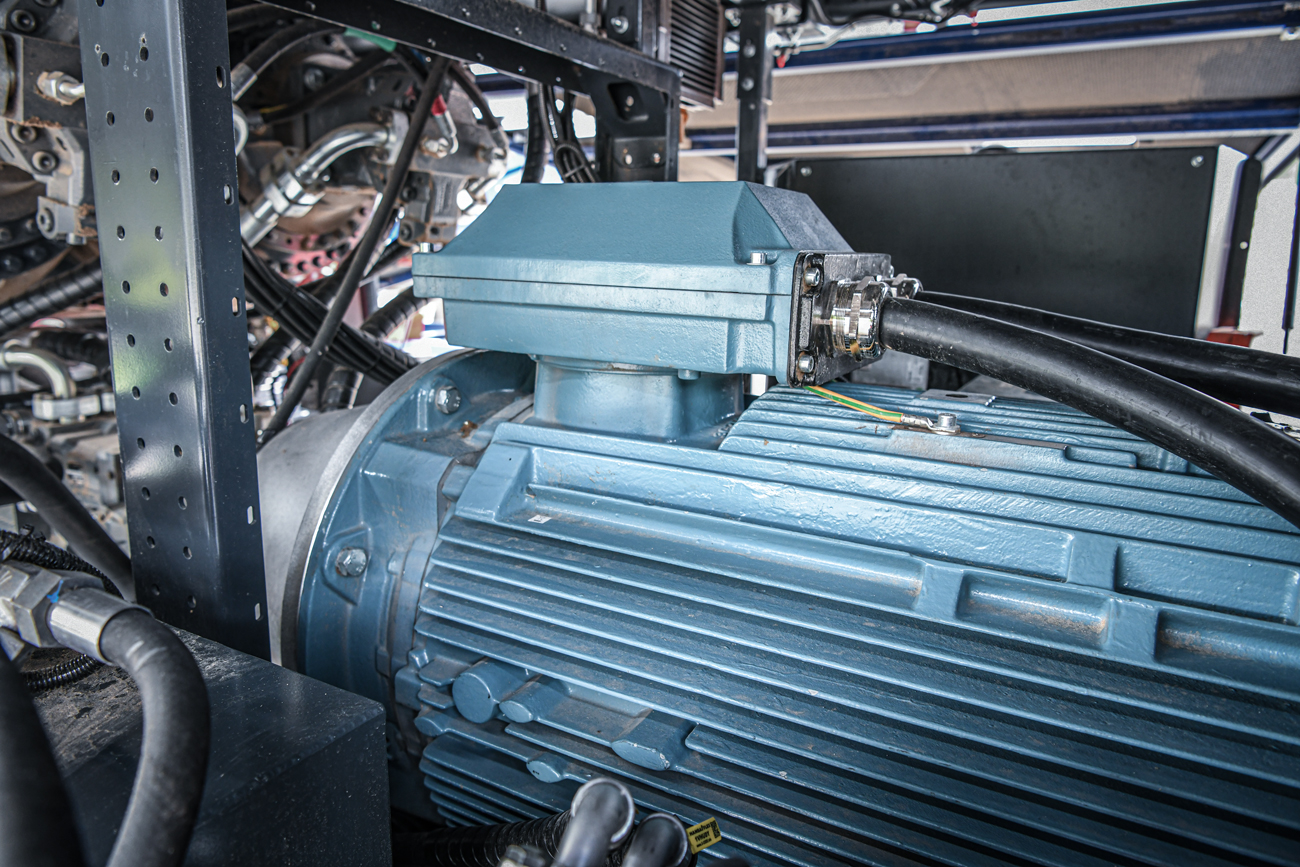
3 | Material Output & FE Metal Separator
WELL-ENGINEERED FEED AND DISCHARGE SYSTEMS
The integrated single-belt discharge conveyor is powered hydraulically and might be completely folded away. The height of the conveyor belt can be easily adjusted during operation by simply lifting the belt from the wheel loader during shredding. For particularly heavy materials such as light scrap and tough commercial waste, the conveyor belt can be reinforced with steel.
- FERROUS METAL SEPARATION with an optional integrated over-belt magnet
- CONSISTENT OUTPUT with our smart double tilting hopper system
- LOW DUST EMISSIONS due to the hydraulic height-adjustable conveyor belt, which can even be adjusted during operation
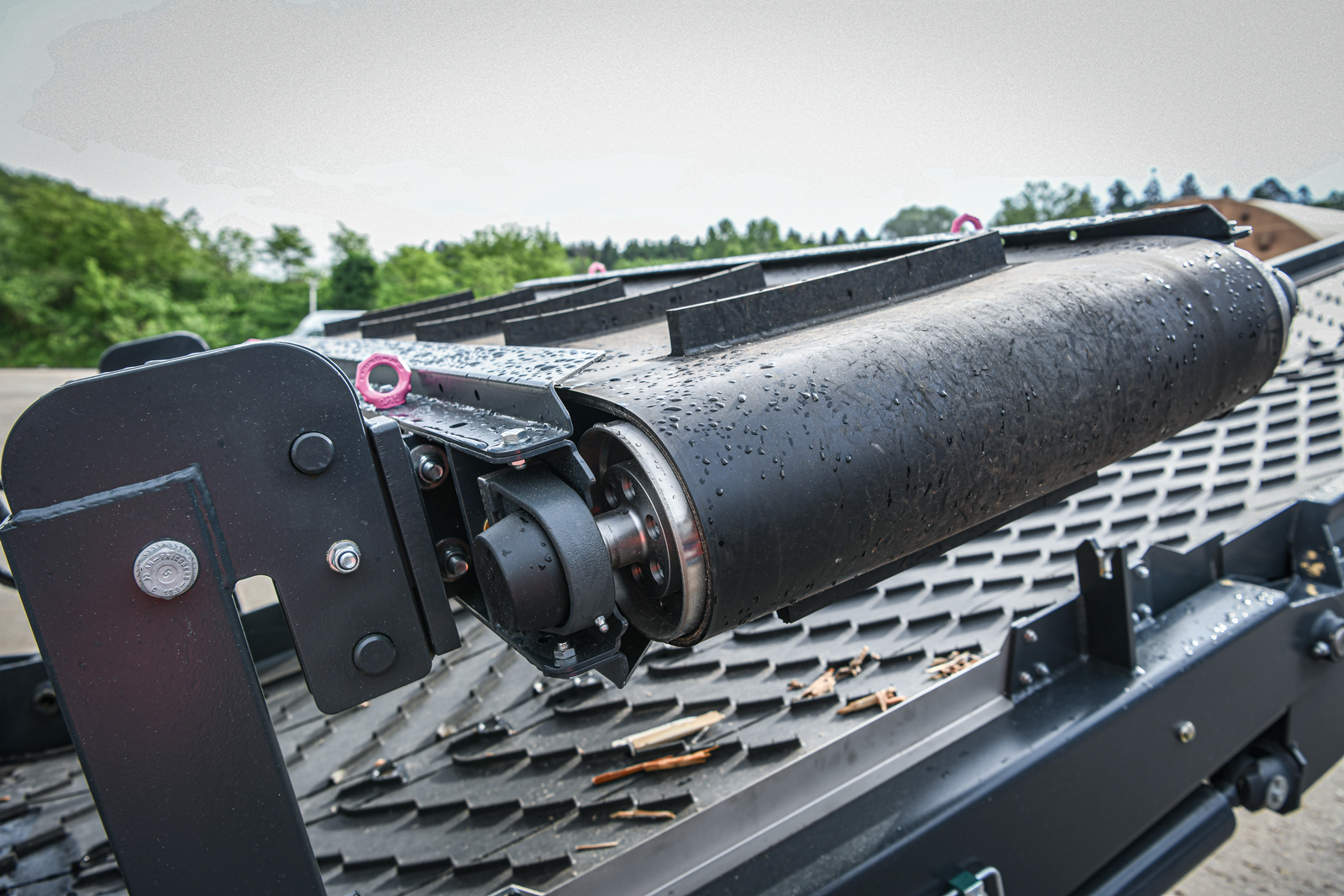
4 | Lindner’s Sky Flap
The Lindner Skyflap is completely removable and allows easy access to the complete cutting room length. The breaker bar can be easily accessed and removed easily with a forklift, enabling fast exchange of the cutting unit. This Lindner Skyflap also allows for quick cleaning of the cutting unit and easy removal of non-shreddables.
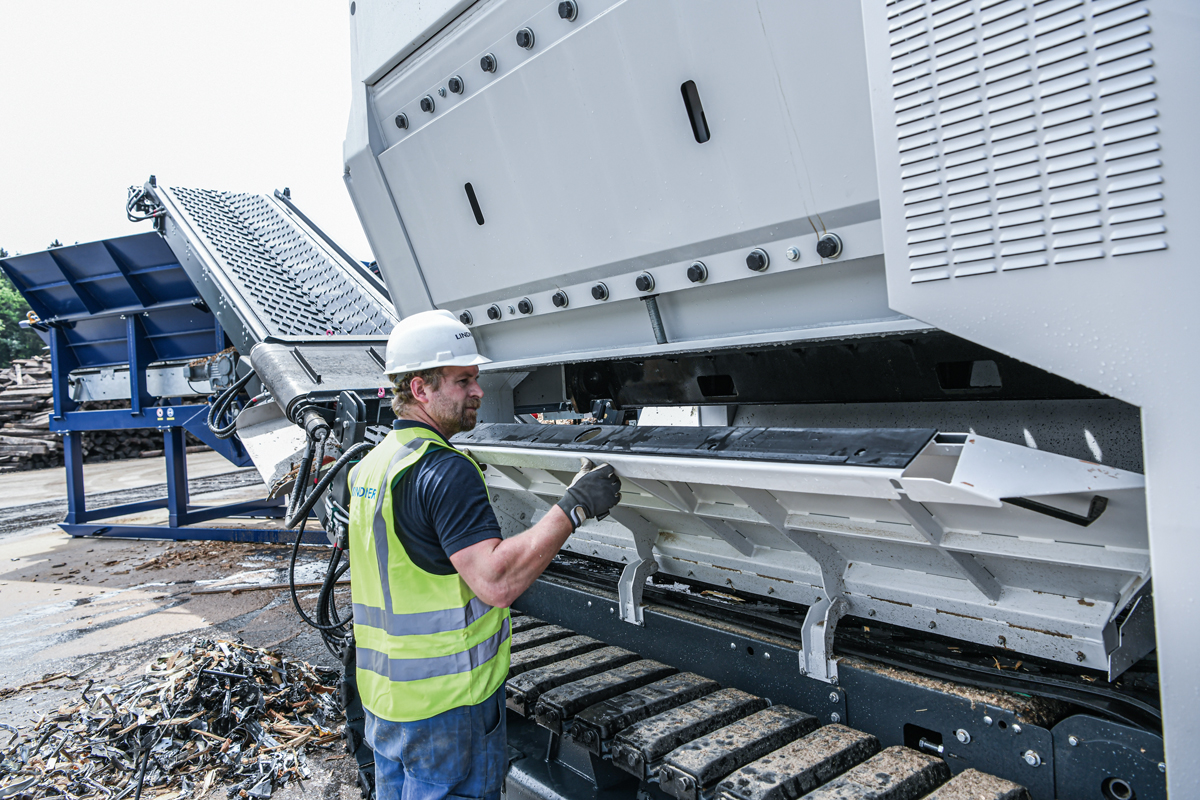
5 | Maintenance door
The Urraco 5000 EKs maintenance door enables even better access to the engine room.
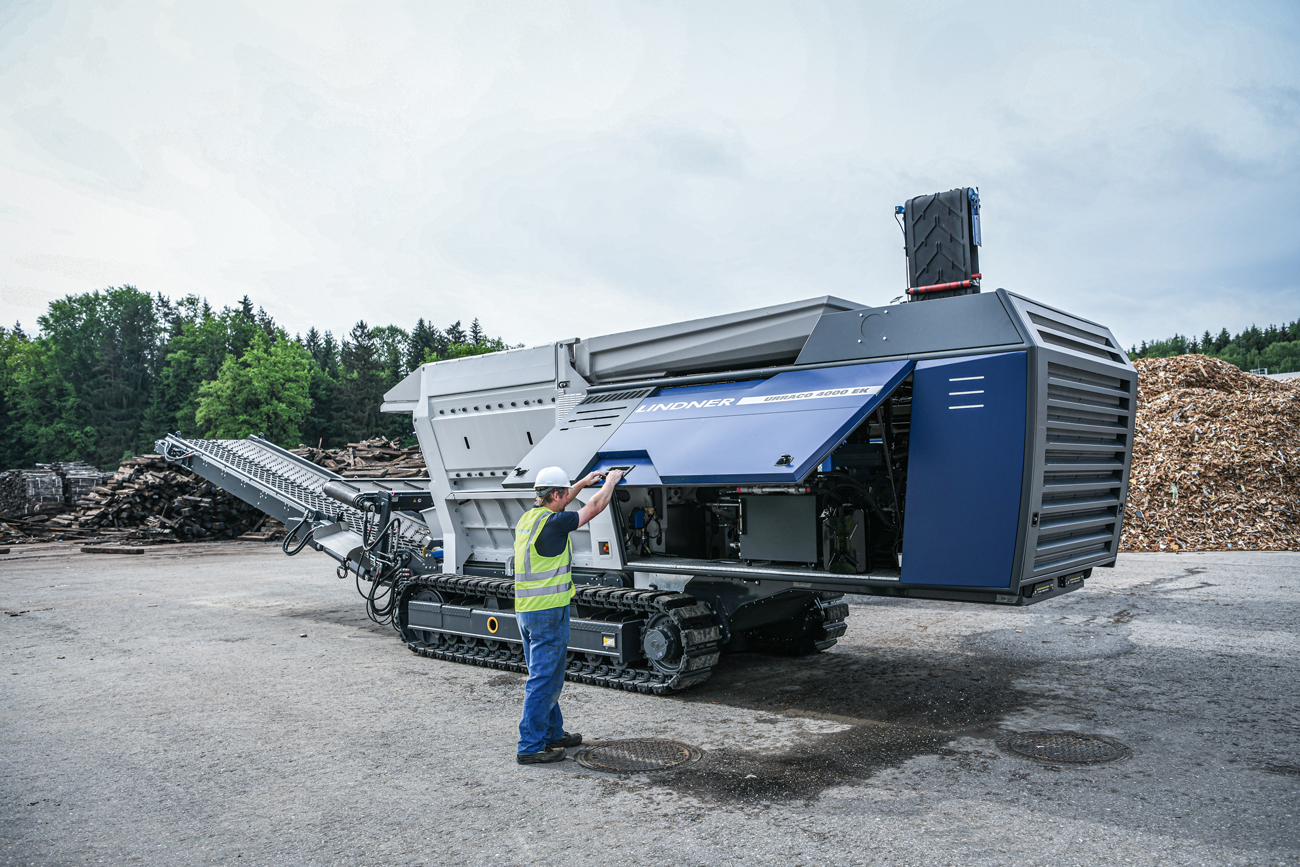
6 | Mobility
The Urraco 5000 EK model is available with a tracked chassis. In addition to its electric engine the Urraco 5000 EK model is equipped with a Diesel aggregate 37kW. This allows for easy repositioning of the shredder to a different location or into the garage.
7 | Operation & handling
Sophisticated control technology with a 7" touchscreen display with 7" and jostick radio remote control for track operations.
- USER-FRIENDLY HMI Bosch-Rexroth controller with intuitive menu
- CONVENIENT shredder operation from the wheel loader using our customisable remote control
- HIGH UPTIMES thanks to our guided fault diagnosis function
- LOCATION-INDEPENDENT, fast software support thanks to our remote maintenance system with integrated GSM module
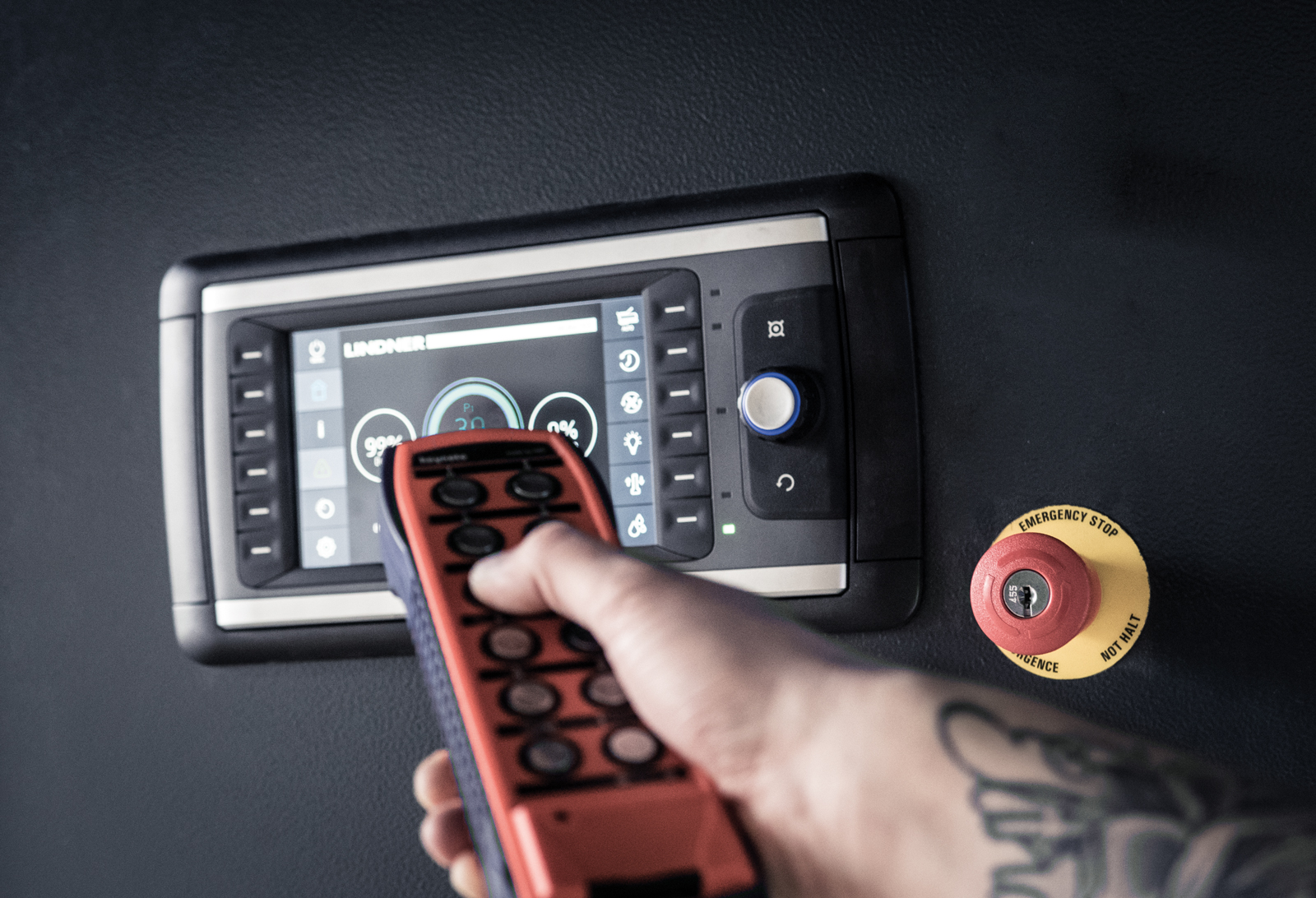
FE metal separator
- Permanent over-belt magnet for ferrous metal separation
- Fitted above the conveyor belt
- Hydraulically height-adjustable
- Incl. discharge chute
Water sprinkling system
- To remove dust from the filling and discharge areas
- 4 pcs. spray nozzles positioned in the suction hood
- 2 pcs. spray nozzles positioned in the output area
- Incl. water filter and pressure limiter
- Switch it ON/OFF using the control pane
Fire extinguishing system
- For effective fire extinguishing in the engine compartment
- Releases cooling and suffocating foam
- Self-monitoring, no electricity needed
- Robust and maintenance-free thanks to galvanised, non-pressurized pipes
Hardfacing Kit
- Ideal for shredding particularly abrasive material
- Knife hardfacing (type HW)
- Scraper hardfacing (type HW)
- Support wire made of cobalt hard alloy
Find your ideal solution and
Connect with us
INPUT & OUTPUT MATERIALS
Waste Wood
C&I | MSW
Light Scrap
Green Waste

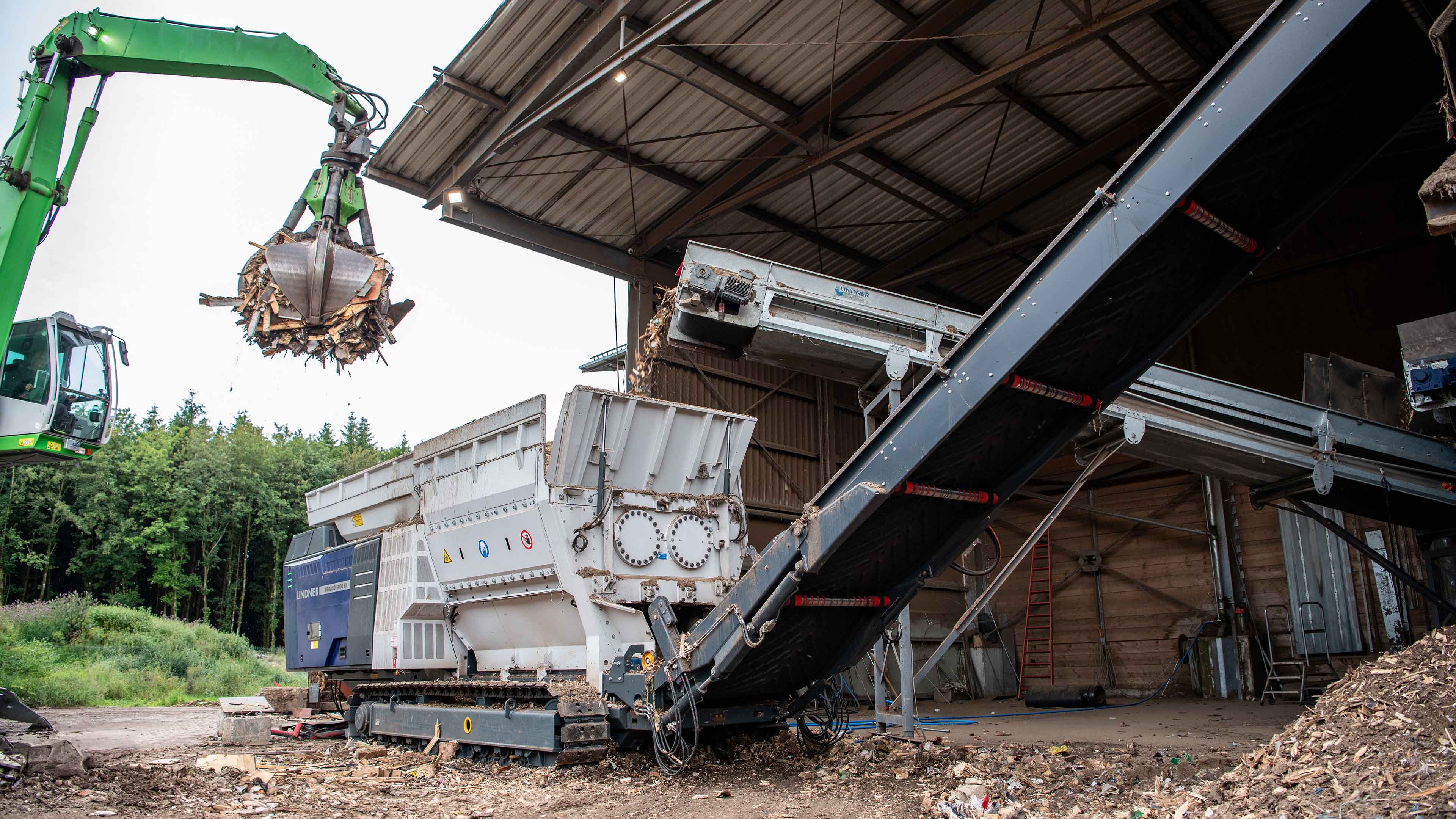
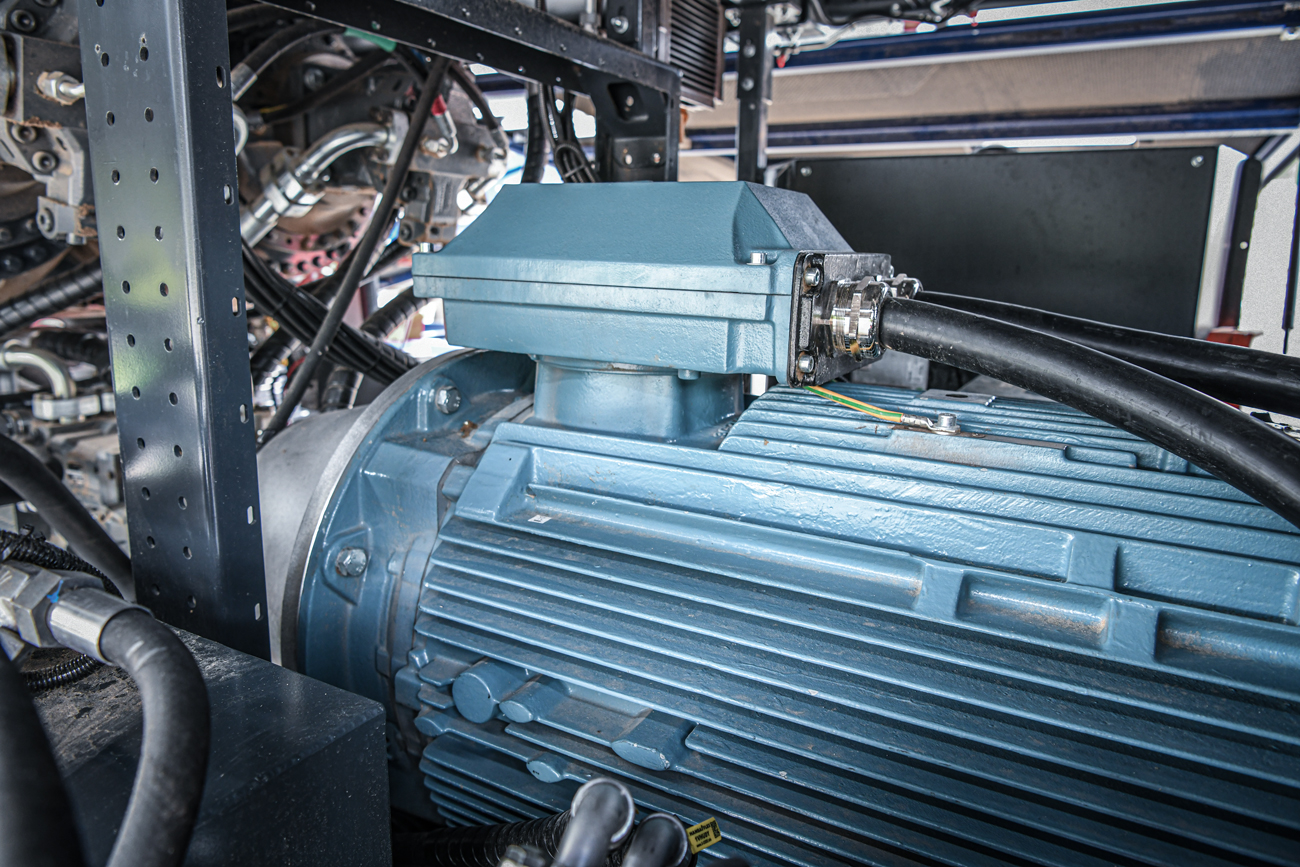
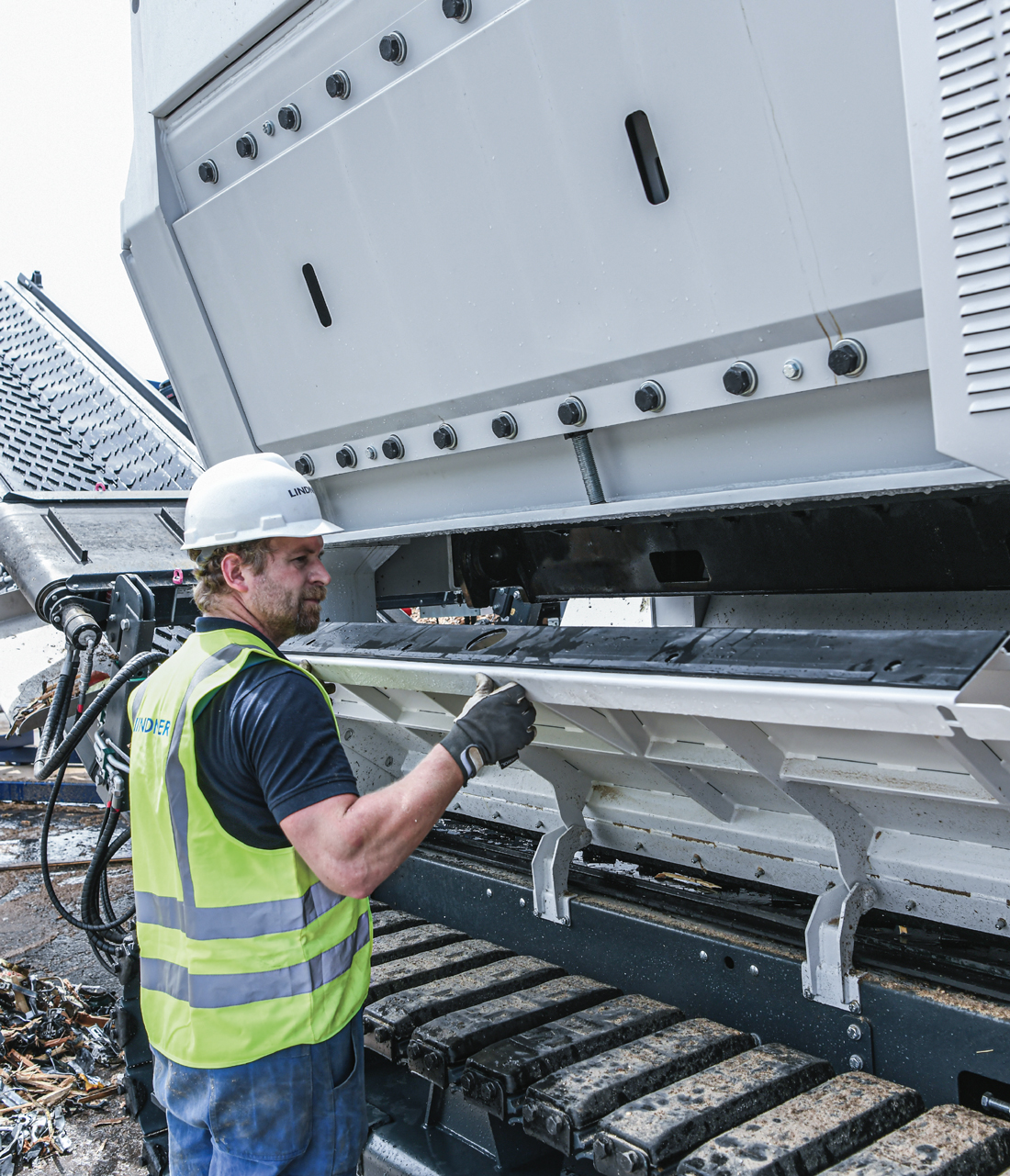
Urraco 5000 EK | |||
Electric drive power | kW | 355 | |
Mobility | Tracked chassis + independent power unit | ||
Shaft length | mm | 2 x 2500 | |
Weight | t | 38 - 41* | |
Dimensions (LxWxH) | mm | 8950 x 2750 x 3250 | |
Discharge height, conveyor (33°) | mm | 4000 / 4850** |
* depending on the machine configuration ** optional