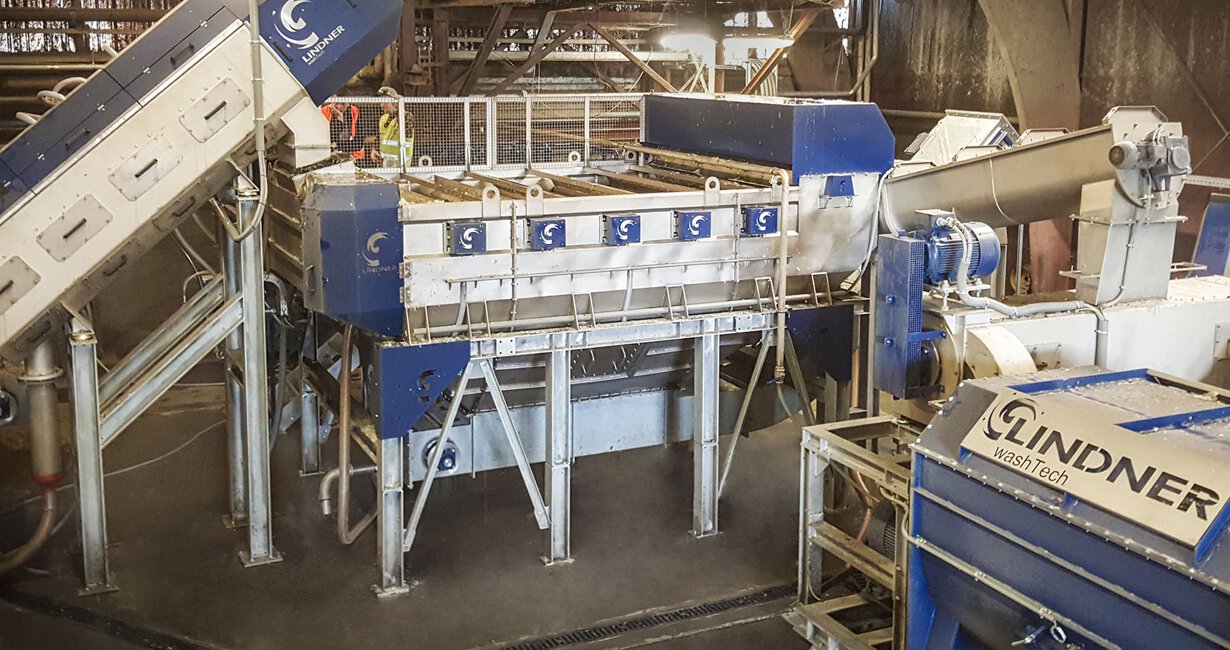
Circular Economy: CeDo gives plastics a genuine second chance
Blown films are highly demanding products, and consequently the use of recycled material in their production represents a major challenge. Impurities in the feed material necessarily lead to production faults that can range from specks and minor defects in the tubular film through to production stoppages. Nevertheless, the CeDo Group, which is based in the English town of Telford and is regarded as one of the European market leaders for bin liners and garbage bags, uses exclusively recycled material in its blown film extrusion lines. It does this out of conviction: „We give the plastics a genuine second chance,“ says Ton Emans, Managing Director of the recycling division at the Dutch site of Geleen. „It only really functions so well because we know exactly how plastics have to be prepared for processing.“ The key to success is the correct washing technology, which is why CeDo Recycling recently purchased a complete washing line from specialists Lindner washTech GmbH from Großbottwar in Germany.
The Lindner Group specialises in the machine technology for the processing of plastic waste – including size reduction, sorting, washing and finally drying. All the components in the chain are tailored to one another and coordinated to the needs of each customer. Precisely for machines that run continuously 24/7, customers need a competent contact partner for the entire process. This is one of Lindner’s key strengths. „Particularly for film waste as is processed here at CeDo Recycling, an efficient centralised control of the overall plant is also key to economic efficiency,“ says Harald Hoffmann, Sales Director Lindner Plastics Division, talking from experience. All the components of the facility can be controlled via a central touch display, and can even be monitored by means of a mobile phone or notebook. „Apart from that, our service engineers in charge of remote maintenance have access to the control system at all times and can optimise the plant to the benefit of the customer,“ says Hoffmann, who also emphasises that the control unit developed by Lindner is quite unique in terms of its ease of operation.
Bin bag production instead of downcycling
With its special service concept and overall machine performance, Lindner was able to fully convince the customer that it was the right partner. CeDo Recycling is the first company to deploy the Rafter pre-washing unit showcased by Lindner at K 2016. This is absolutely typical of recycling pioneer CeDo, which frequently opts for innovations. When it was founded around 40 years ago, the company was one of the first to operate a PET recycling facility and it was also the first company, a few years later, to use a friction washing machine for treating post-consumer waste and was also, in turn, the first to opt for the NIR technology for sorting the residual materials. „We are pioneers when it comes to plastics recycling and above all as regards the quality of the produced regrind material, and we want to keep it that way,“ says Ton Emans, who is very proud indeed of his team of 54 employees who, just like him, are 100 % behind this common interest. „Without such a committed team, we could not do such good work,“ he says, and continues: „Our joint aim is to protect the environment and to make good use of existing resources.“ And for this, they have also chosen the most difficult fraction of residual materials: Film residues from the DSD fraction 310, which were initially downcycled or incinerated. CeDo Recycling has shown that the in some cases heavily contaminated post-consumer film waste can be turned back into film, in this case for the production of bin liners and garbage bags on blown film lines. „In our production plants in Poland and England, we produce a variety of different film sizes for a very wide range of bags, with which we supply 30 major retailers in Europe. The product spectrum also includes bin bags from recycled material produced from extruded blown film with a thickness of 22 µm,“ says the Production Manager of the recycling company, Peter Vranken, not without a certain amount of pride. „These garbage bags have the lowest CO2 footprint that is currently available.“
Rapid installation of the overall solution
In order to attain the high output quality needed for blown film extrusion, the CeDo Group‘s recycling plant in Geleen operates various washing units, the youngest of which was engineered and installed by Lindner washTech. This was done within a very short time window defined by the customer and with a limited amount of space. „We had very precise idea of the new plant, which not only had to be perfectly integrated into our existing infrastructures, but also had to be ready for use within the shortest possible time,“ admits Ton Emans and praises his supplier: „Lindner washTech proved to be a very reliable and punctual partner, who satisfied our demands completely.“ Peter Vranken adds: „We are very pleased indeed with the present solution and are convinced that this is a washing unit equipped with the most sophisticated technology on the market.“
The starting element of the overall unit is a chain-type conveyor that picks up the supplied film bales and conveys them to the pre-shredder, a Jupiter 1800. Here, a rotor with 145 x 145 mm blades opens the bales and undertakes an initial shredding to produce pieces of film as uniform as possible with a size of around DIN A4. The material is then taken to an 80 m3 material bunker in order to ensure a constant material flow for the subsequent NIR sorting. Via a ballistic screen, fines smaller than 30 mm are separated off, and the pre-shredded films are then conveyed through two NIR sorting stations, where the LDPE films are, in the first step, sorted positively and in the second step, negatively. „This results in 99 % purity of the necessary material fraction, which will later guarantee the high quality of the CeDo products,“ says Peter Vranken. The sorted fraction is then taken to the Komet 2800 single-shaft shredder, which, with a throughput of 6 t/h, reduces the pieces of film to smaller particles with a size of around 30 mm in a single step. Characteristic of the Komet are its rugged and low-maintenance work mode and its individual adjustability. The counter-knives, which can be adjusted easily and quickly, ensure precise cutting and, like the rotor blades, are readily accessible thanks to the famous Lindner maintenance flap. All in all, it is a very economical solution, particularly as no downstream cutting mill is required, thus saving further costs and space.
Rafter ensures high economic efficiency
After the shredding, the film flakes are conveyed to the Rafter. This latest new development from Lindner washTech works with an innovative concept in which the material does not – as is usually the case – float on the water but is effectively cleaned under water. „The unwanted substances and the particles adhering to the plastic that are heavier than LDPE sink in the washing zone and are directly separated off,“ explains Harald Hoffmann. The advantage is that these separated solid materials are eliminated during the first processing step and do not have to be separated off in a complicated procedure during water treatment. „Every hour, around 100 kg of contaminants and particles adhering to the plastic like sand are separated off in the Rafter. The washing process in the Rafter is not only highly effective, it is also, because of the gentle process, not subject to disruption and wear and tear, which in turn benefits the overall efficiency of the unit. After a friction washer and the graviter, in which the separation is made by density, the material flow is split up into two lines and taken to the mechanical dryers. This is where the final cleaning – e.g. to eliminate paper residues – and subsequent thermal drying to approx. 6 % residual moisture takes place. The cleaned material is then conveyed to silos where it is homogenised and is thus ready for re-extrusion. CeDo processes more than 100,000 tons a year into film for bin liners and garbage bags. Around a third of its input material for this is produced by the company itself in its modern and economical washing and processing plants. It goes without saying that the quality must be absolutely right.